Custom Gear
For 25 years Exegi has been trying to build boards and skis that are better. Boards that are more durable, have better performance, and are therefore more enjoyable to use. What has become undeniable is that the most important factor in achieving better boards and skis matching the performance envelope of the gear to the rider. Everything else is secondary. And we’re here to do exactly that for you. Click the button to start designing your own board or skis.
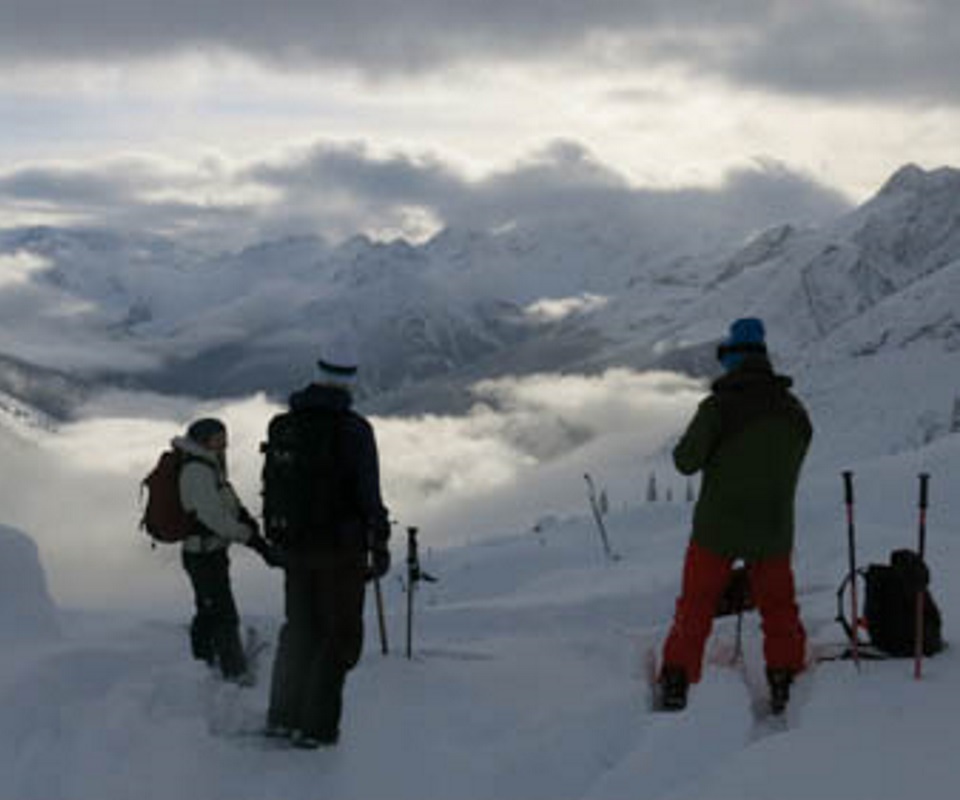
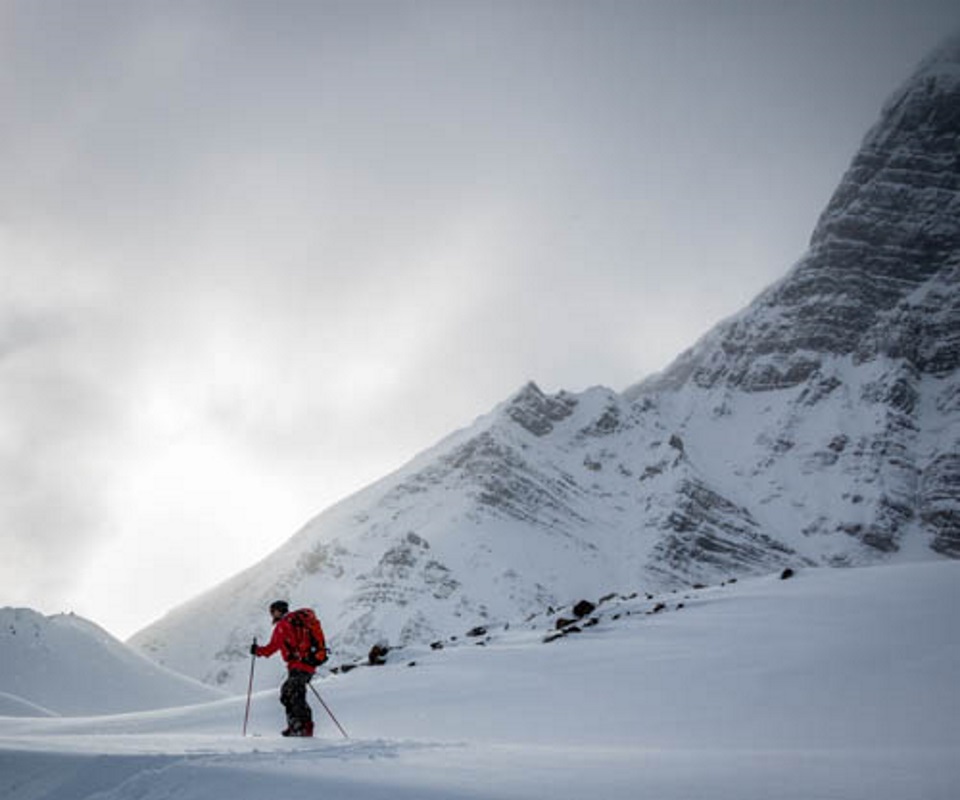
Our Technology
Exegi offers boarders, splitboarders, and skiers a unique combination of attributes that ensures that each rider gets the best board or skis for them. We build our equipment out of carbon fiber and use innovative and effective technologies to maximize performance. We commit to matching our gear to your individual requirements. Click the button to learn more about how our tech works for you.
Carbon Fiber
Exegi uses carbon fiber to build its custom boards and skis. Appropriately used carbon fiber is something of a miracle material. Check out some of the benefits:
RESPONSIVENESS
The highly directional nature of carbon fibers allows for nearly infinite variations in tuning flex, and the production of skis and boards that are responsive and fun to ride
LONG LIFECYCLE
Our carbon fiber equipment is fatigue resistant and keeps its as-good-as-new qualities longer than fibreglass or metal
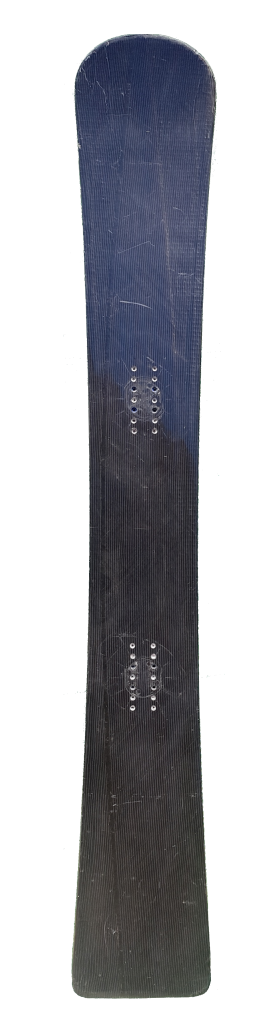
DAMAGE TOLERANCE
The carbon fiber and epoxy configuration in our skis and boards can handle the wear and tear of riders pushing their limits
BLEEDING EDGE
Carbon fiber is the go-to material for all kinds of high performance manufacturing, including auto racing, bicycles, tennis, aerospace, tennis and golf